David Karmeli has worked for five years on his latest, and likely, final turntable design, The Absolute Nothing. The name is based on the idea that the turntable does not add or remove anything from the information imbedded in the record groove. This is an ultra high mass thread drive design and the culmination of what David has learned about turntable design over the past several decades. To improve on the AS2000 design, he had to go to extremes.
Here are some of the details: The platter weighs 300 lbs. The base weighs about 600 lbs, the motor unit weighs about 100 lbs. The stand, an integral part of the design, weighs another 350 lbs or so. The motor casing is machined from a single block of stainless steel. It is the same Pabst motor as in the AS2000, but now has a three phase motor controller. Rather than the five digit speed display, the new turntable has a strobe on the platter. The massive platter floats on a cushion of air, just like the AS2000. The platter is wider and taller but can be driven easily by the thin thread for minimal contact with the motor pulley/flywheel. The massive base has an irregular pattern of facets on its surface that are designed to control the internal resonances in the base and draw them away from the platter. There are isolation devices integrated into the motor unit, the stand, the arm mounts, and the footers. The motor controller has a worm-drive mechanism that allows one to adjust the thread tension. Motor torque and speed can be fine tuned. Everything is designed with a purpose.
I first saw drawings for this turntable a couple of years ago. David has been working on this for the last five years. CDK84, a fellow WBF member, and I visited the factory and met David a month ago, and then again last week to oversee the move from the factory to the first owner's listening room. After helping to assemble the turntable, David set up the SME 3012R tonearm and Neumann cartridge.
It was clear from the moment the Neumann stylus hit the first groove that this turntable takes the presentation to the next level. There is an uncanny calmness. The presentation is utterly relaxed yet somehow full of energy. The music comes alive in the room and the musicians are present in front of the listener. What this turntable does better than any other turntable I have heard is remove the sense that there is anything mechanical between the listener and the performance captured on the record. My AS2000 does this very well, but The Absolute Nothing takes it further by a margin I did not think was possible.
There is nothing in the presentation that is emphasized, just the ease of the performers in the room. My simple take is that the bass primarily, but also the rest of the information on the record is not corrupted or obscured by the mechanical nature of other turntables. There is more information that comes through to the cartridge and tonearm. When the arm and cartridge are at the level of the 3012R and the Neumann, it seems as if all of the music captured in the vinyl comes through, at least more than I have heard from any other table. There is just more of everything presented naturally. Nothing seems missing because there is just so much more music flowing forth.
I listened until 5:30 in the morning and left for Boston a couple of hours later driving for hours to hear a chamber concert of harp, flute, and strings later that night. Having heard the new turntable in an all Lamm Signature and Karma Midi Grand Exquisite system, followed so closely by a live chamber concert, it is clear to me that David has narrowed the gap between the live and reproduced pretty dramatically.
"Nothing between the listener and the recording" - David's description gets to the essence of this new turntable. It is also what is behind his approach to system set up. David Karmeli has achieved something truly remarkable here, and I could see his satisfaction as he listened. The pride of a designer working hard and then achieving success. I feel fortunate to have witnessed it and heard it as he did for that first time.
Three videos:
Here are some of the details: The platter weighs 300 lbs. The base weighs about 600 lbs, the motor unit weighs about 100 lbs. The stand, an integral part of the design, weighs another 350 lbs or so. The motor casing is machined from a single block of stainless steel. It is the same Pabst motor as in the AS2000, but now has a three phase motor controller. Rather than the five digit speed display, the new turntable has a strobe on the platter. The massive platter floats on a cushion of air, just like the AS2000. The platter is wider and taller but can be driven easily by the thin thread for minimal contact with the motor pulley/flywheel. The massive base has an irregular pattern of facets on its surface that are designed to control the internal resonances in the base and draw them away from the platter. There are isolation devices integrated into the motor unit, the stand, the arm mounts, and the footers. The motor controller has a worm-drive mechanism that allows one to adjust the thread tension. Motor torque and speed can be fine tuned. Everything is designed with a purpose.
I first saw drawings for this turntable a couple of years ago. David has been working on this for the last five years. CDK84, a fellow WBF member, and I visited the factory and met David a month ago, and then again last week to oversee the move from the factory to the first owner's listening room. After helping to assemble the turntable, David set up the SME 3012R tonearm and Neumann cartridge.
It was clear from the moment the Neumann stylus hit the first groove that this turntable takes the presentation to the next level. There is an uncanny calmness. The presentation is utterly relaxed yet somehow full of energy. The music comes alive in the room and the musicians are present in front of the listener. What this turntable does better than any other turntable I have heard is remove the sense that there is anything mechanical between the listener and the performance captured on the record. My AS2000 does this very well, but The Absolute Nothing takes it further by a margin I did not think was possible.
There is nothing in the presentation that is emphasized, just the ease of the performers in the room. My simple take is that the bass primarily, but also the rest of the information on the record is not corrupted or obscured by the mechanical nature of other turntables. There is more information that comes through to the cartridge and tonearm. When the arm and cartridge are at the level of the 3012R and the Neumann, it seems as if all of the music captured in the vinyl comes through, at least more than I have heard from any other table. There is just more of everything presented naturally. Nothing seems missing because there is just so much more music flowing forth.
I listened until 5:30 in the morning and left for Boston a couple of hours later driving for hours to hear a chamber concert of harp, flute, and strings later that night. Having heard the new turntable in an all Lamm Signature and Karma Midi Grand Exquisite system, followed so closely by a live chamber concert, it is clear to me that David has narrowed the gap between the live and reproduced pretty dramatically.
"Nothing between the listener and the recording" - David's description gets to the essence of this new turntable. It is also what is behind his approach to system set up. David Karmeli has achieved something truly remarkable here, and I could see his satisfaction as he listened. The pride of a designer working hard and then achieving success. I feel fortunate to have witnessed it and heard it as he did for that first time.
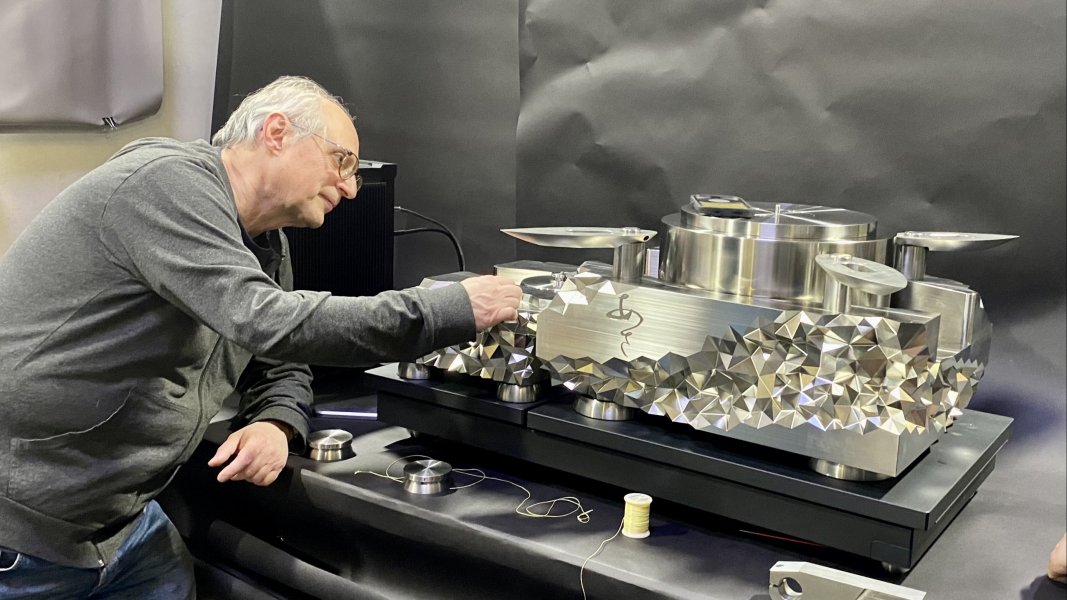

Three videos:
Attachments
Last edited: